Business strategies for integrated management for companies with a high level of manufacturing offer a panoramic view of the production processes in order to develop an optimal planning phase by phase.
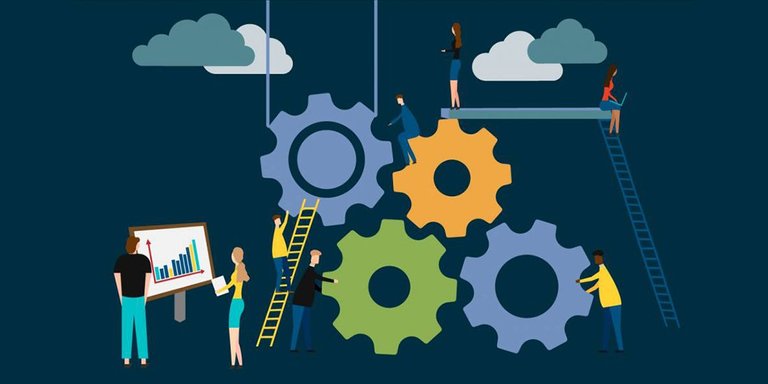
Subsequently, when the cost elements are added, a statistical record is kept of the inputs consumed in each order and accumulated in a format known as a cost sheet. The cost sheet specifically identifies an order and contains the respective spaces to accumulate the raw material, labor and indirect costs consumed for that order.
Costs are recorded as the order moves through the different production departments. Once the production process has been completed, the cost sheet shows the total accumulated cost of the order and, therefore, the unit cost of the product.
Among the many characteristics of the work order costing system are the following: each work order is assigned a sequential number that allows the identification of the cost sheet, which includes the three elements of the cost of production.
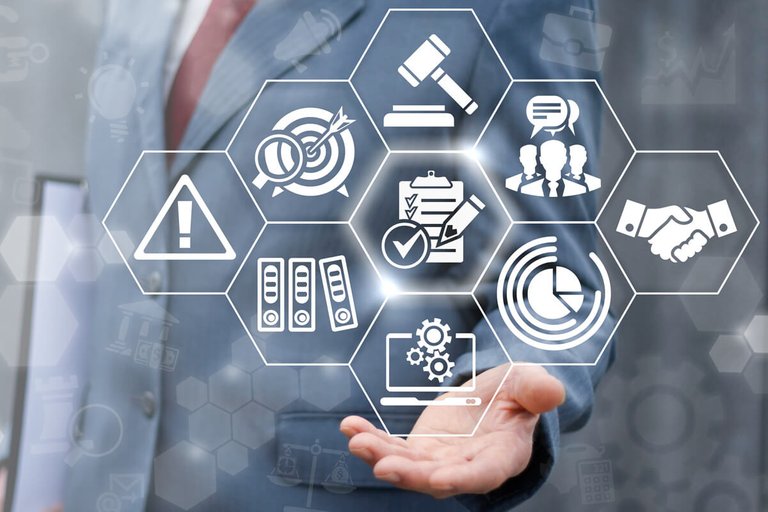
The cost sheet of the respective work order accumulates the costs incurred to produce that order. The costing unit is the work order, the cost of finished products is obtained by adding the costs accumulated in the cost sheets of the finished orders.
Congratulations @alaiza! You have completed the following achievement on the Hive blockchain And have been rewarded with New badge(s)
Your next target is to reach 70000 upvotes.
You can view your badges on your board and compare yourself to others in the Ranking
If you no longer want to receive notifications, reply to this comment with the word
STOP
Check out our last posts:
Support the HiveBuzz project. Vote for our proposal!